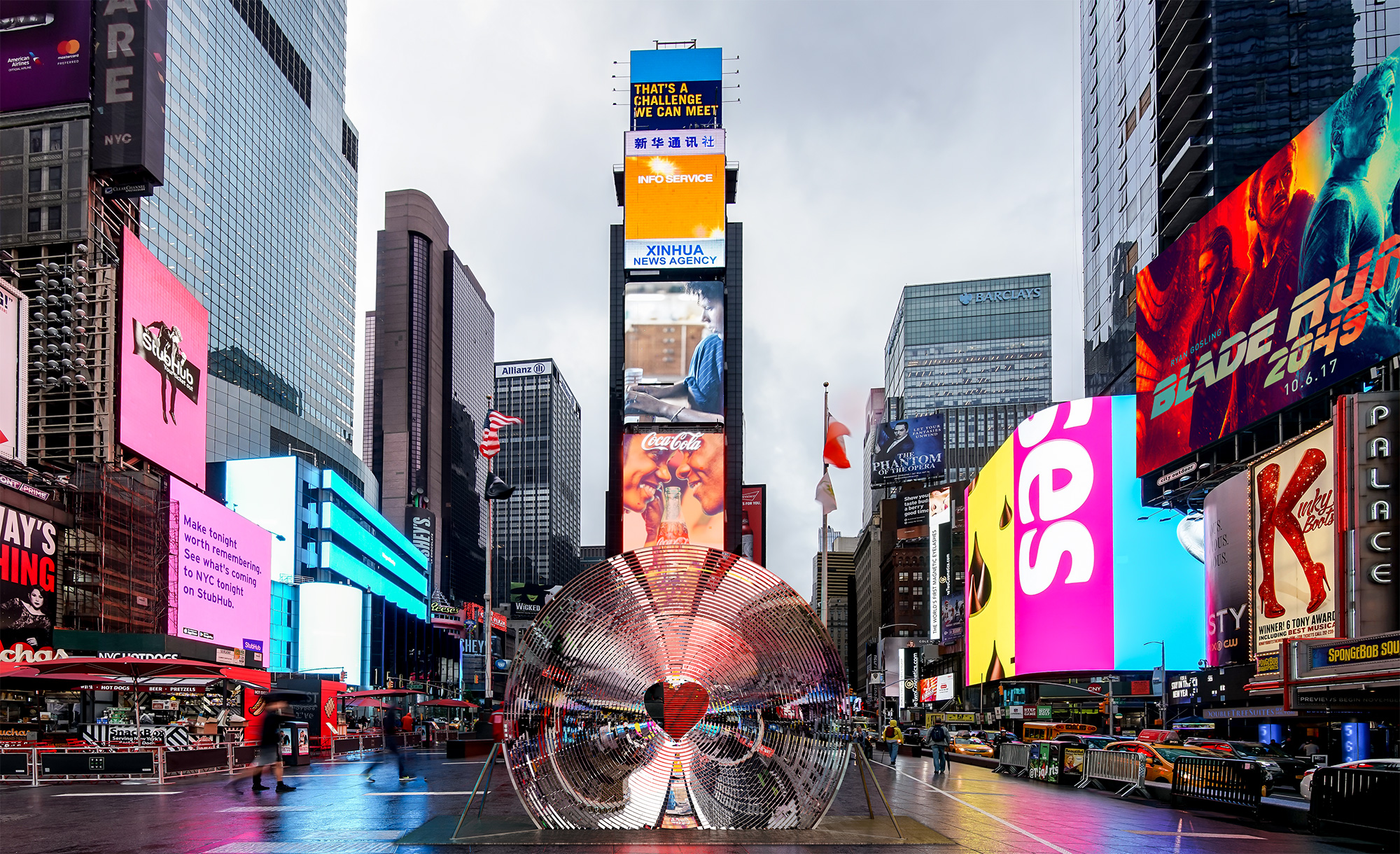
Generally speaking, we don’t see Instagram bait and boundary-pushing science and technology in the same art project—never the twain shall meet.
But today in Times Square (of all calm, thoughtful spots) the architect and designer Benjamin Aranda of Aranda/Lasch is debuting Window to the Heart, an interactive public art project that has seriously forward-leaning ideas and techniques behind it.
The 4,500-pound piece is a huge lens—in fact, by a couple of inches it ranks as the World’s Largest Lens—with a heart-shaped cutout in the middle.
The core is a massive piece of clear acrylic stuck onto a steel base that can survive a hurricane. Some 1,000 grooved pieces of hard resin that were created by 3D printers have been glued onto both sides of the acrylic. Seen together, the lens will create striking distortions of shape and light.
Window to the Heart, on view until March 1, was commissioned by Times Square Arts and the Design Trust for Public Space, which does a Valentine’s Day–themed project every year (this its 10th anniversary), hence the cute heart shape, perfect for photos. And yes, the first wedding in front of the project has already been booked.
Aranda wanted to honor that lovey-dovey theme, but complicate things a bit to and keep it interesting for himself and his partners, which included the Boston-based 3D printing company Formlabs and Caliper Studio of Brooklyn, which hosted the fabrication.

“When we went to Times Square to think about it, we noticed that everyone is photographing billboards, and there are a lot of selfies,” says Aranda. “A lot of cameras out. People are using small screens to take pictures of big screens—and behind all those screens is a lens.”
It got him thinking about the layers involved. “The Iens is the unsung hero of our media-saturated world,” he says. “The optics of seeing —your eye has a lens, too”
So he contacted Formlabs and they cooked up a plan that wouldn’t have been possible with technology from a year ago. First they researched the largest lens in the world, which was in a lighthouse in Hawaii, and thought they could go a little bigger.

After the design was complete, they had 50 3D printers running 24/7 for two weeks to make the lens pieces. The machines—which are like little orange R2-D2s, shaking a bit as they spit out their product—consumed 300 liters of resin. “It’s a Herculean effort to show where 21st-century manufacturing is at now,” says Aranda, who blew threw the $35,000 commission budget long ago. They put in extra time and effort because of sheer “maker bravado,” jokes Marcelo Coelho, the director of design at Formlabs.
Last week on Caliper’s shop floor, team members were busily and carefully gluing on the lens pieces to the acrylic core. If they’re not perfect, the desired visual effects—essentially, a warping of light and image toward the center opening—won’t happen. “It’s a nerve-wracking project,” says Aranda. But he couldn’t resist noting the level of their commitment, too: “I guess you could say we put our heart in it.”